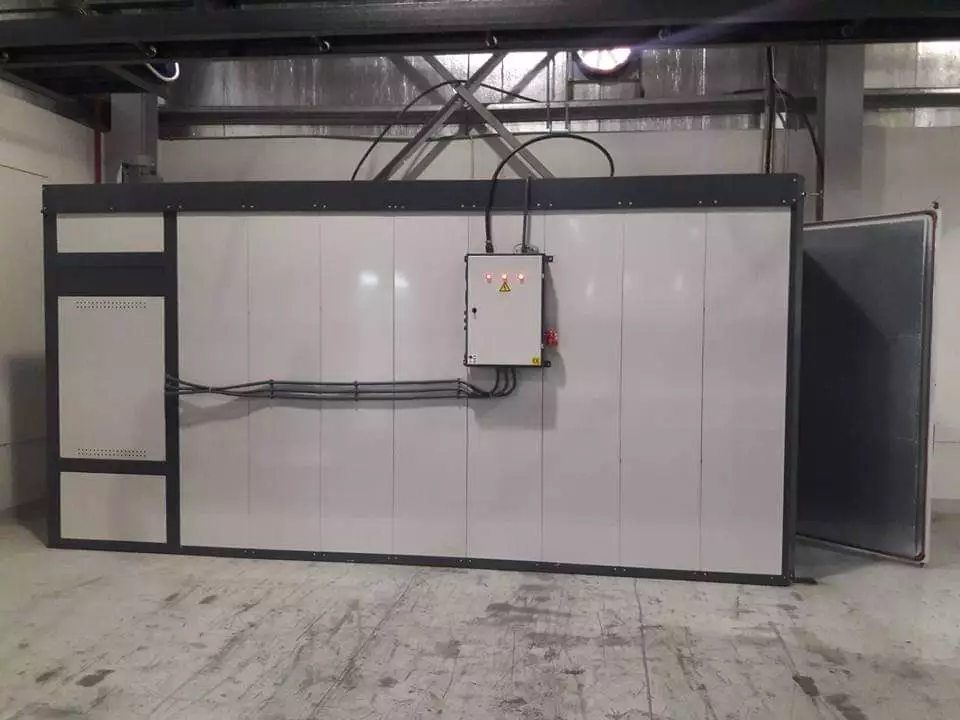
Post Preview
Industrial powder coating ovens are all about efficiency, durability, and delivering top-notch finishes. These ovens work by heating the coating powder to a high temperature, creating a hard, protective layer on the metal surfaces inside. But keeping all that heat contained can be quite a task. Without effective heat containment strategies, energy costs rise, and the quality of the coating can suffer. So, how do these massive ovens manage to keep their heat locked in? Let’s dig into some of the key strategies that ensure maximum efficiency in industrial powder coating ovens.
Multi-Layered Insulation to Keep the Heat Locked In
One of the most effective ways to maintain heat in powder coating ovens is through multi-layered insulation. Think of this insulation like a thick blanket that keeps the oven’s heat from escaping. Each layer serves a different purpose, but together, they work to ensure consistent internal temperatures and energy efficiency. The layers are made of materials that resist high temperatures and help trap the heat inside, preventing energy loss.
Multi-layered insulation also improves safety in the workplace. By minimizing heat loss to the oven’s exterior, it reduces the risk of accidental burns for operators working nearby. Plus, it allows the oven to heat up faster and maintain steady temperatures during the coating process. This results in better, more uniform finishes for powder-coated parts, keeping customers happy and production running smoothly.
Smart Door Seals That Prevent Heat Leakage
Even with solid insulation, heat can still find sneaky ways to escape—like through the oven doors. That’s where smart door seals come into play. These seals are specially designed to prevent heat from leaking out whenever the doors open or close. Made of heat-resistant materials, they can handle high temperatures without degrading, ensuring they stay effective for a long time.
The beauty of smart door seals is that they adapt to the oven’s temperature changes. When the oven heats up, these seals expand slightly, filling any gaps and creating a tight seal that keeps the heat locked inside. This simple yet effective strategy can make a big difference in energy efficiency and overall oven performance.
Strategic Heat Zone Separation for Maximum Containment
Inside a powder coating oven, different areas may require different temperatures. This is where strategic heat zone separation becomes essential. By dividing the oven into distinct zones, operators can control the heat levels more precisely in each area. This helps maintain optimal temperatures throughout the oven, reducing the chances of overheating or underheating certain sections.
Heat zone separation not only aids in energy efficiency but also supports the quality of the final coating. By ensuring that each zone is at the right temperature, manufacturers can achieve a more even and consistent coating on the products. This strategy also allows for quicker adjustments if any zone needs a temperature change, making it easier to handle a variety of parts with different coating requirements.
Optimized Wall Thickness to Maintain Internal Temperatures
The thickness of an oven’s walls plays a huge role in heat containment. Thicker walls generally mean better heat retention, as they can hold in more heat for longer periods. This helps maintain steady internal temperatures, making the oven more efficient and cost-effective. In industrial powder coating ovens, manufacturers often design the walls to be both thick and made from materials that resist high temperatures, creating a thermal barrier that minimizes energy loss.
Optimized wall thickness doesn’t just improve heat retention; it also prolongs the life of the oven. With the heat safely contained, the oven’s components experience less wear and tear, reducing maintenance costs and downtime. This makes optimized wall thickness a win-win for energy efficiency and longevity.
Heat-Reflective Coatings to Bounce Energy Back Inside
Heat-reflective coatings are a clever way to keep the heat where it belongs—inside the oven. These coatings, usually applied to the interior surfaces, work by reflecting the heat waves back into the chamber, rather than allowing them to be absorbed by the oven walls. This simple yet effective method helps maintain consistent temperatures and reduces energy consumption.
By using heat-reflective coatings, manufacturers can ensure that the powder coating oven heats up more quickly and retains that heat longer. The result is not only a more efficient heating process but also better-quality finishes on the coated products. Plus, with less energy required to maintain high temperatures, this approach can lead to lower energy costs over time.
Controlled Ventilation for Minimizing Unwanted Heat Loss
Ventilation is a necessity in powder coating ovens, but it can also be a source of unwanted heat loss if not managed properly. Controlled ventilation systems are designed to maintain proper airflow while keeping heat inside the oven. These systems use strategically placed vents that allow for the necessary release of fumes or moisture, without letting too much heat escape.
This approach helps maintain a balanced temperature inside the oven, ensuring consistent heating and coating quality. By controlling ventilation, operators can also reduce the risk of overheating, which can damage parts or create safety hazards. With the right balance, controlled ventilation keeps the heat contained, making the oven more efficient and safer for everyone involved.
More Stories
Enhance Your Garden Sunbathing Experience with Essential Home Backup Power
The Growing Need for Easy and Reliable Global Connectivity While Travelling Abroad
Top 5 AI-powered social media management tools for event organizers